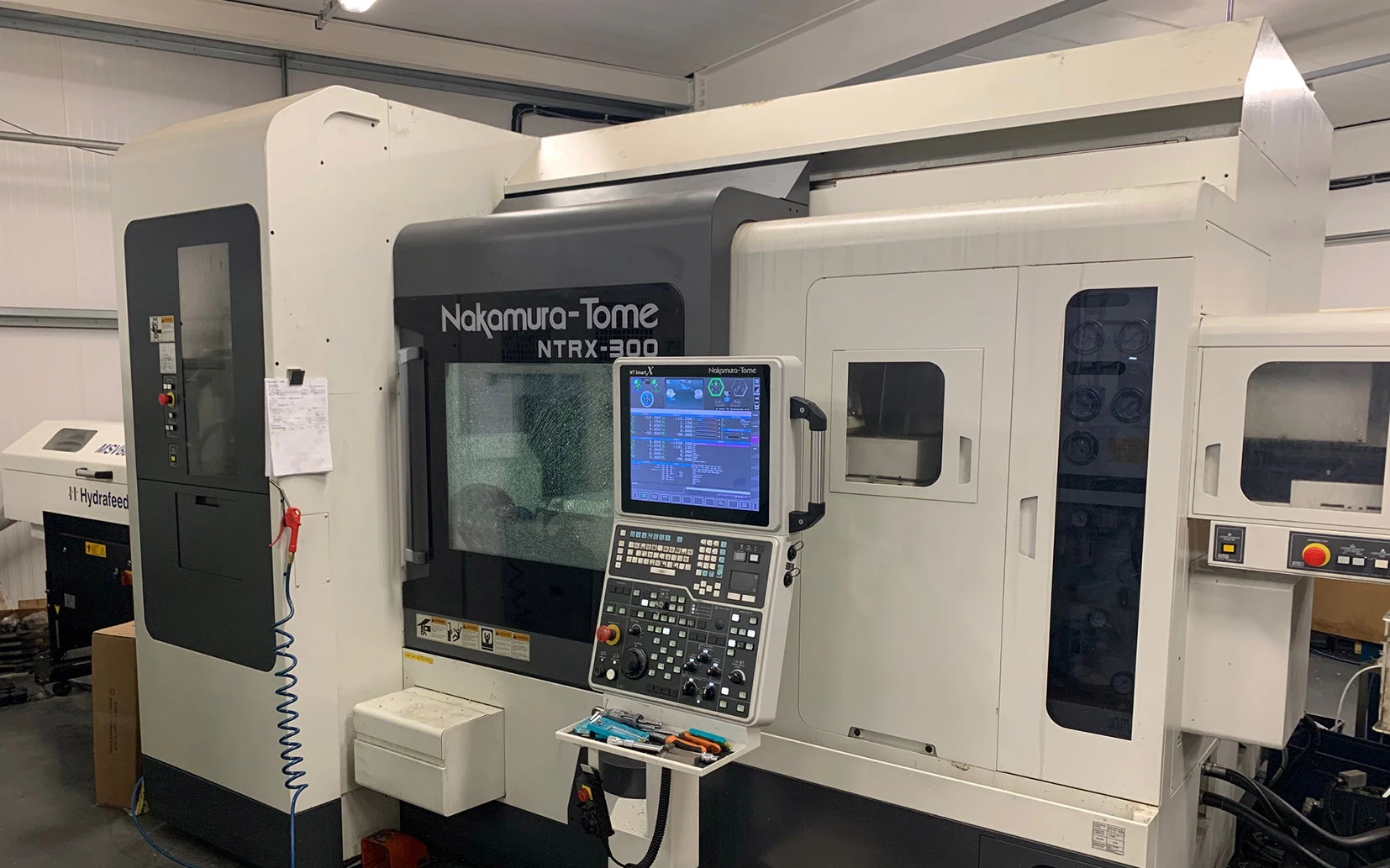
Member Article
Nakamura investment helps Rotec Engineering achieve ‘lights-out’ manufacturing
A specialist supplier of complex components has completed a £450,000 investment drive with the purchase of the latest 5-Axis technology to reduce set-up times and achieve ‘lights-out’ manufacturing.
Rotec Engineering, which offers aerospace, automotive and oil gas customers advanced fixed head and sliding head capabilities from its facility in Evesham, has installed a new Nakamura NTRX 300 from the Engineering Technology Group (ETG), building on a long-term relationship with the machine tool supplier.
“It is a great machine. We’ve been involved with Nakamura for some time and its technology is extremely reliable, very fast and very accurate,” explained Paul Butler, Managing Director and owner of Rotec Ltd.
“In our endeavour to move forward and expand, we wanted a machine with all of these attributes that we could also programme directly from our CAM programme with full 5-axis turning.”
He continued: “We found that just focusing on cycle time wasn’t the right way forward for our business. There is often a lot of downtime between jobs, so the whole idea of this investment is to apply the CAM system and the machine flexibility to reduce our set-up times.
“Now, we can set-up complex jobs very quickly and, with a bar feed and auxiliary loader, we can run these challenging parts unmanned and they come off the machine complete.
“As a company we have made a paradigm change in the way we work, investing £450,000 into embracing Industry 4.0 principles and integrating advanced technology into our manufacturing facility, achieving autonomous running of complex parts.”
ETG, which is the UK’s exclusive supplier of Nakamura technology, worked with Rotec to source a machine that matched its exact requirements, with the NTRX 300’s milling head and two rotating spindles proving extremely attractive.
The challenge was to get all the technology to work seamlessly for the company so that it trusts the machines to run when employees aren’t there. This meant that during the day staff can set-up complex, automotive and F1 parts, whilst during the night they can look at processing parts that, historically, would be milled components.
ETG’s Steve Brown concluded: “Our technical experts are increasingly taking on a number of ‘lights-out’ production projects each month, where we will work with sub-contractors to explore the possibility of producing components through the night without any labour costs.
“Advancements in technology and our strong relationships with leading software providers means this scenario is not purely the property of the big boys, with millions of pounds set aside to introduce it. No, instead SMEs from all sectors are now switching on to the benefits this new industrial trend can bring, Rotec being a great example of that.”
This was posted in Bdaily's Members' News section by Russ Cockburn .
Enjoy the read? Get Bdaily delivered.
Sign up to receive our popular morning National email for free.