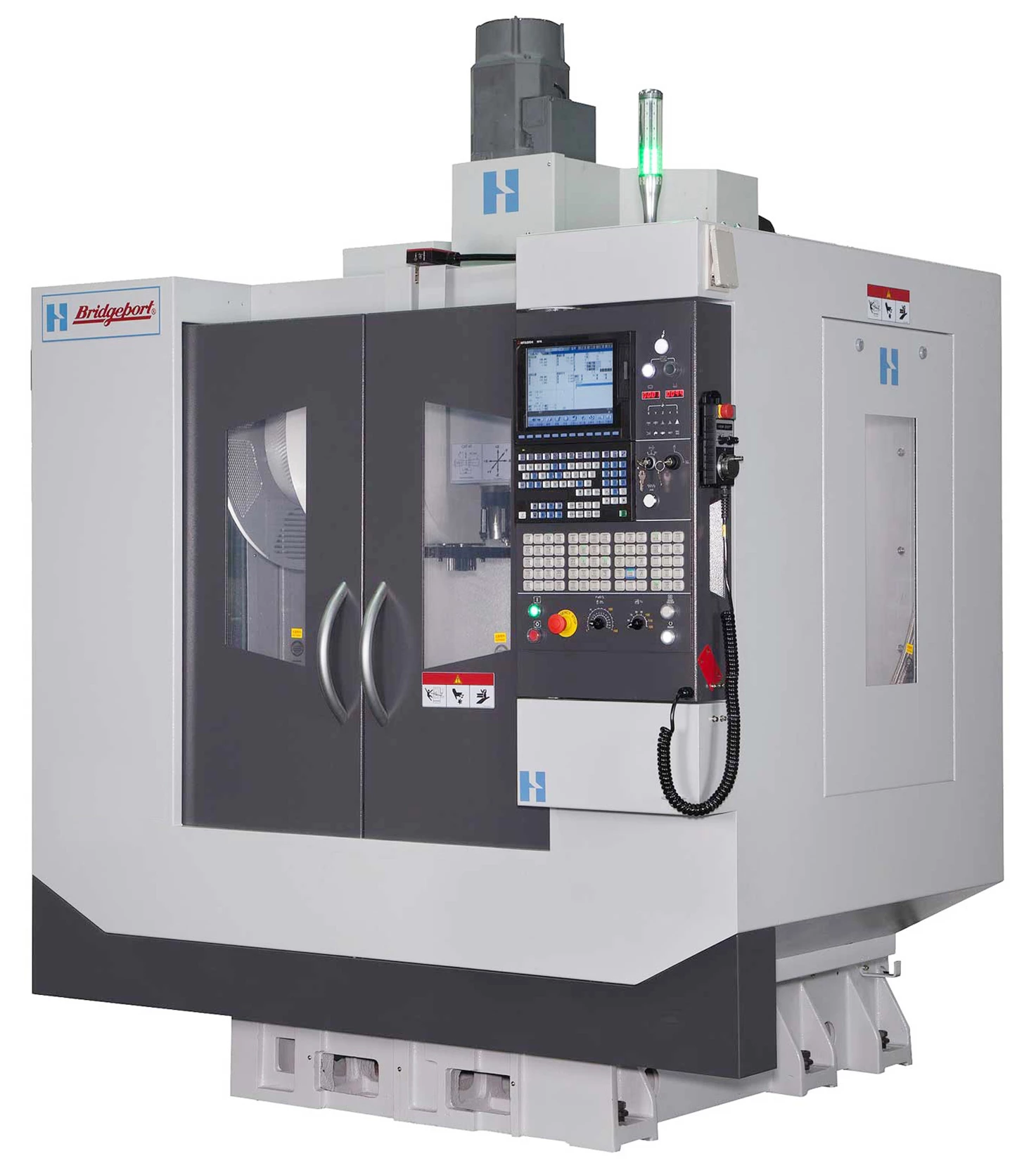
Partner Article
Spalding engineering firm maintains its haul of orders with new CNC machine technology
The huge growth in fish farming in recent years is proving good news for a small precision engineering company based near Spalding.
A one-off job a decade and a half ago has turned into a major stream of business for Channing Engineering, which employs eight people at its workshop in the village of Pinchbeck.
Run by Colin Channing, the company makes parts that are in high demand for fish farming businesses in Norway, the Faroe Islands and in Canada. As a result, more than half of its work is now exported and, unlike many currently, the firm has no worries about the implications of Brexit with all of its main sales destinations outside the EU.
With business continuing to grow due to its reputation for quality and reliability, Mr Channing and his team have decided to replace one of their Bridgeport machining centres, working with the Engineering Technology Group (ETG) to purchase a new Hardinge GX710S.
“The previous machine was a highly reliable piece of kit, so it made sense to get another Bridgeport,” pointed out Colin.
“It has been a while since we’ve had to replace a piece of equipment and it was the first time we have worked with ETG. Everything went very smoothly and, when any issues did crop up, we received a rapid response, which is just what you want with a significant investment.”
The Bridgeport Hardinge GX710S is a three-axis vertical machining centre with 20 tools on an ATC carousel and a single spindle speed of up to 12,000rpm. Table size is 800 x 400mm and the X/Y/Z axis offers 710/400 and 430mm.
It has been equipped with Siemens controls to provide optimum accuracy and allow for fast transfer of data.
Colin added: “We are very busy at the moment, with most of our work involving short runs of a few dozen parts off a time, or one-off prototyping.
“Whilst we cover a wide range of different industries, including components for racing cars, fish farming equipment is still the biggest single source of work for us. The first piece of work we got, probably 15 years ago, was for Norway and we found we were quoting £100 a piece less than the other firms they were talking to.
“We now make our own version of some components and, as an industry, it now accounts for around 60 per cent of our workload, supplying customers in Norway, the Faroe Islands and Canada. It has just snowballed.
“And there’s no sign of a slowdown. Fish farming has been the fastest growing sector of the food industry for the last two decades and global farmed fish production is expected to expand by a third by 2026.”
Jon Mannion, Regional Sales Manager at Engineering Technology Group, added: “This machine comes with Siemens’ ShopMill software and has a small footprint, which suited the company. Colin was already aware of the brand’s reputation for speed and reliability and he was impressed with the build quality.
“It ticked all the boxes for Channing Engineering and we were able to get it delivered very quickly as the firm needed it in operation as soon as possible.”
Engineering Technology Group (ETG) delivers highly productive turnkey solutions to customers involved in automotive, aerospace, domestic goods, high value engineering, medical and oil and gas.
Its portfolio of world class brand includes Bavius, Chiron, Nakamura, Quaser and STAMA.
This was posted in Bdaily's Members' News section by Russ Cockburn .