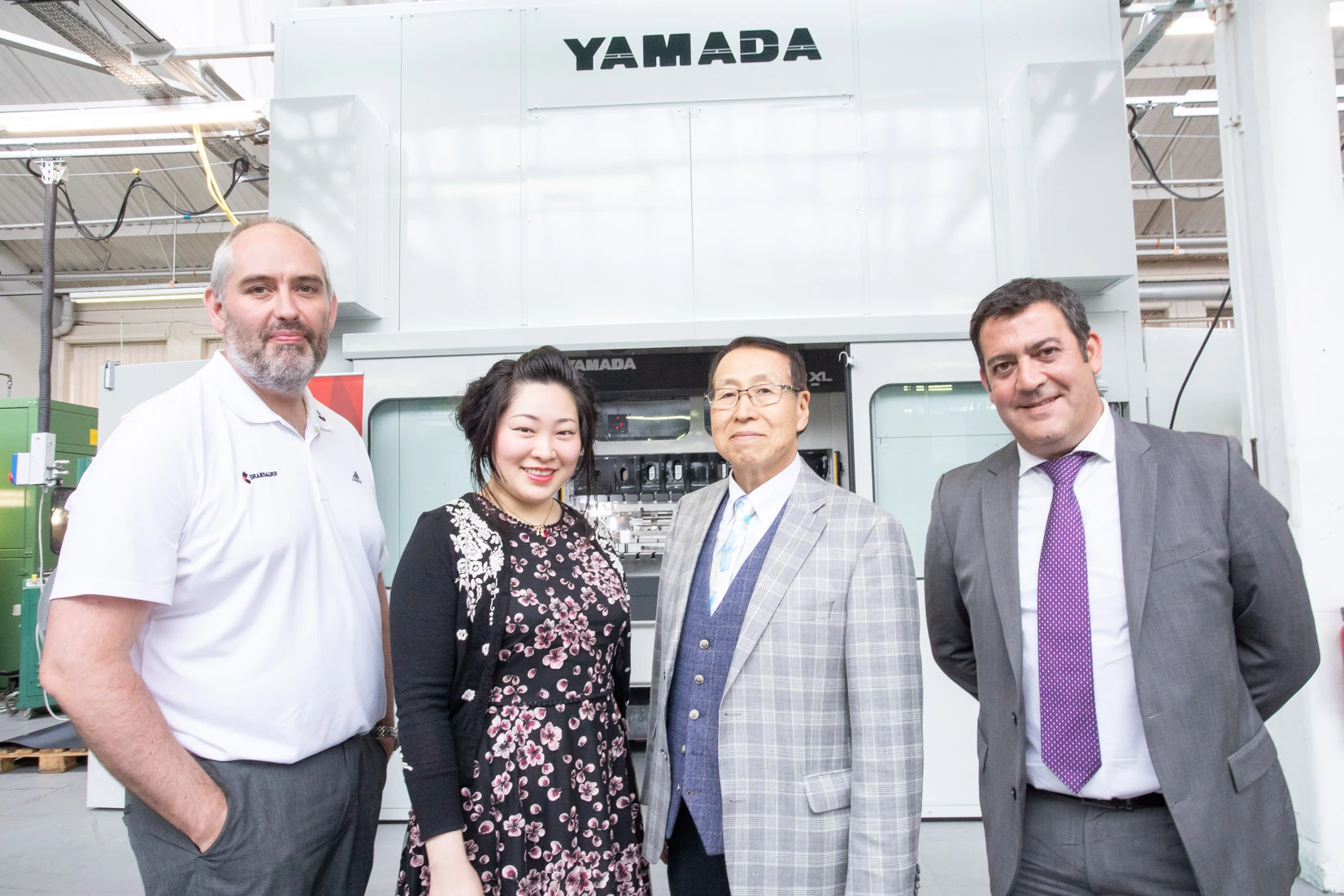
Member Article
Brandauer taps into Japanese technology with £600,000 high-speed press investment
Investment in a new high-speed press is set to help a Birmingham metal stamping specialist capitalise on 20% growth over the last twelve months.
Brandauer, which recently secured a Queen’s Award for International Trade, has spent £600,000 on a Yamada Dobby NXT 80XL as part of a three-year plan to boost its capacity and provide additional production flexibility.
The state-of-the-art technology gives it patented repeatability on quality and a 100% reduction in press setting time that frees up manufacturing space to take on new contract wins in the plumbing sector, automotive motor laminations and fuel cells.
It is the first machine it has purchased from the Japanese-based press specialist and it tops off a £2m modernisation of its Birmingham facility that has also included a new GF wire cut EDM machine, 2 Andmar surface grinders and an OGP Smartscope Vantage 250 to help with quality inspection.
Don Walters, Operations Manager at Brandauer, commented: “We first came across the press at Blechexpo and were impressed with what we saw in terms of its speed, the repeatable quality and how user friendly it appeared.”
He continued: “Our visit to its showroom in Italy gave us the chance to see the Yamada in all of its glory and we worked with its experts to configure the machine so it delivers the accuracy and performance we were looking to achieve.”
Established in 1862, Brandauer is one of the West Midlands best kept manufacturing secrets, producing millions of high tolerance metal pressings and stampings every week for customers in the plumbing, automotive, domestic products, electrical, medical and renewables sectors.
It took just 9 months from the order being placed for the Yamada NXT 80XL press to be installed and commissioned, with the machine now working on components that use material ranging in thickness from 0.2 to 0.8mm.
The 1.5m metre bed is the largest the company currently has available and it can operate at speeds of between 100 and 800 strokes per minute.
Karl Jeavons, Press Shop Team Leader at Brandauer, went on to add: “The quality is second to none and we run off thousands and thousands of parts every day, thanks in part to the double link motion mechanism that delivers Yamada’s patented repeatability, whilst also helping to prolong the life of the tool.
“What has really impressed us is how easy the press is to set-up and use, reducing the set-up time in some instances from 3.5 hours to 6 minutes. This is due to the simple user interface, which is capable of storing up to 1000 different set-ups. Once the initial setting work is done a semi-skilled setter can take over for all future runs of the same product.
“This massively frees up resource, giving us the ability to move our engineers on to different projects so that we can run jobs simultaneously.”
He concluded: “Other benefits that the Yamada delivers, includes proven low maintenance, excellent standard-fit equipment and SMED and Industry 4.0 capabilities to futureproof the press going forward.”
Building on the first installation, Brandauer’s world class manufacturing environment has been assigned as a technology showcase partner for Yamada Dobby, with a number of open houses planned for later in the year.
This was posted in Bdaily's Members' News section by Russ Cockburn .