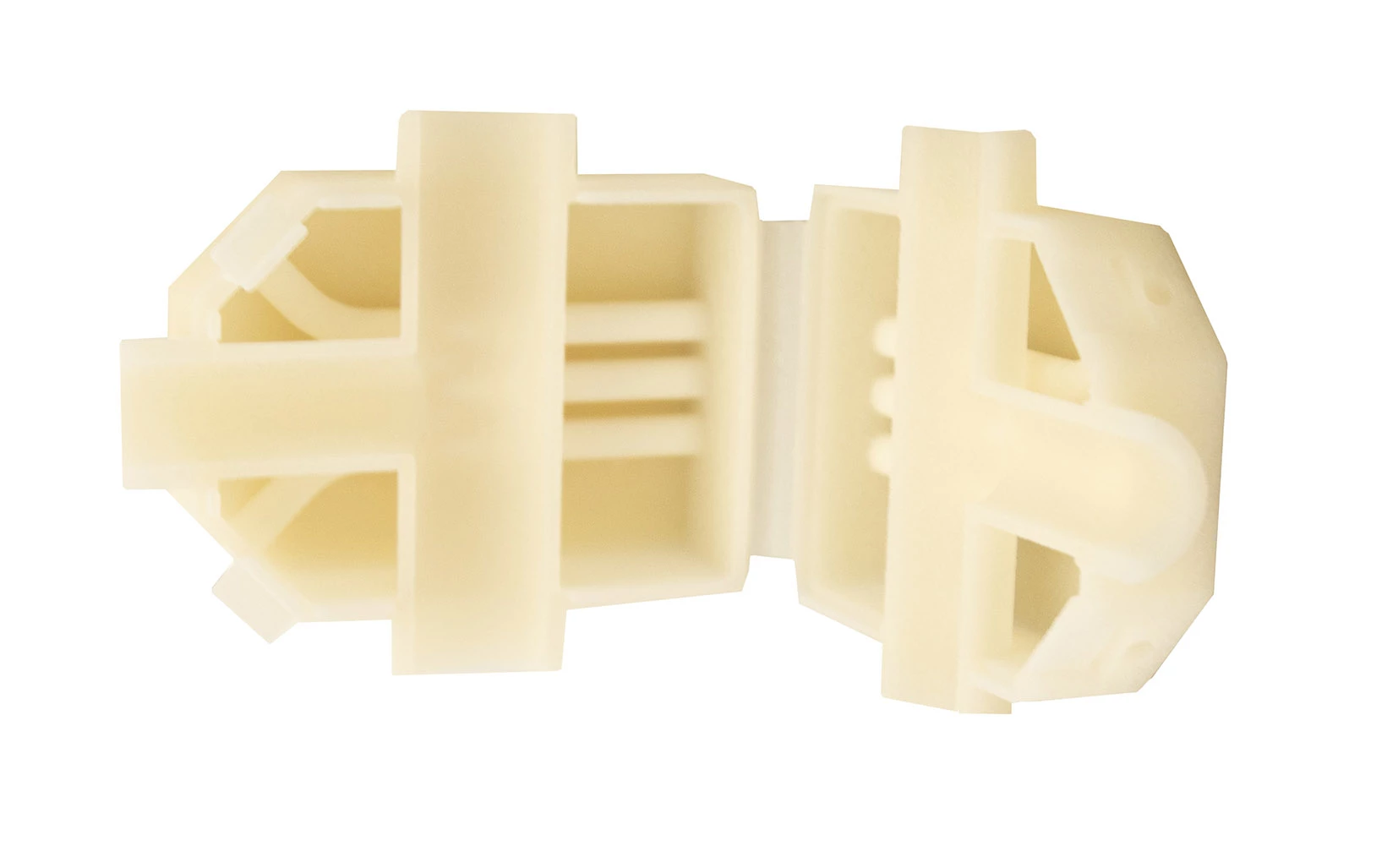
Member Article
Protolabs launches polypropylene 3D printing service in Europe
World-leading digital manufacturer Protolabs has launched polypropylene 3D printing in Europe, the first time it has offered this service.
The Telford-based company has invested significantly into developing this new material for use in selective laser sintering, which will give design engineers the opportunity to develop and test prototypes rapidly. It also allows for complex designs to be produced using 3D printing, previously impossible in this material.
“Polypropylene is one of the most used plastics available to modern manufacturers and is widely used for a number of applications,” explained Andrea Landoni, 3D printing product manager for Protolabs.
“Until recently you could only use 3D printed polypropylene-like materials that mimicked this plastic, but they did not have all of the same properties and were not as durable.
“Now that we can produce a prototype in polypropylene, design engineers can develop and test it in an application using the same material that it will be manufactured from. The product design can then be quickly reiterated and retested until they have the perfect solution, before committing to tooling.
“This breakthrough takes product development to the next level using the most versatile of plastics.”
3D printing polypropylene opens up a whole host of designs with complex geometries that were previously impossible, such as honeycomb structures to reduce weight or organic shapes such as internal channels.
“Before, if you wanted to use polypropylene then you were limited in what you could design by the manufacturing technology available to you. Now the only limitation is your imagination,” continued Andrea.
“There are many times, however, when the best solution for a manufacturer may be to produce polypropylene parts using injection moulding or CNC machining. We can give you unbiased advice on which is best to use because we now offer all three manufacturing technologies.”
Protolabs helps manufacturers through the complete product development cycle, from initial prototype to checking that the final design is suitable for mass manufacture using its Design for Manufacture Analysis software. This is available for both injection moulding and CNC services.
As the world’s fastest digital manufacturing resource, the company can also offer on-demand production using bridge tooling for injection moulding while the manufacturer waits for their full production moulds.
Andrea concluded: “In an age where speed to market really counts, Protolabs can significantly reduce the lead time for a new product or part from initial concept right through to final manufacture. With this new service, we can help manufacturers get new polypropylene products to market weeks or even months earlier than before.”
For further information, please visit www.protolabs.co.uk.
This was posted in Bdaily's Members' News section by Russ Cockburn .