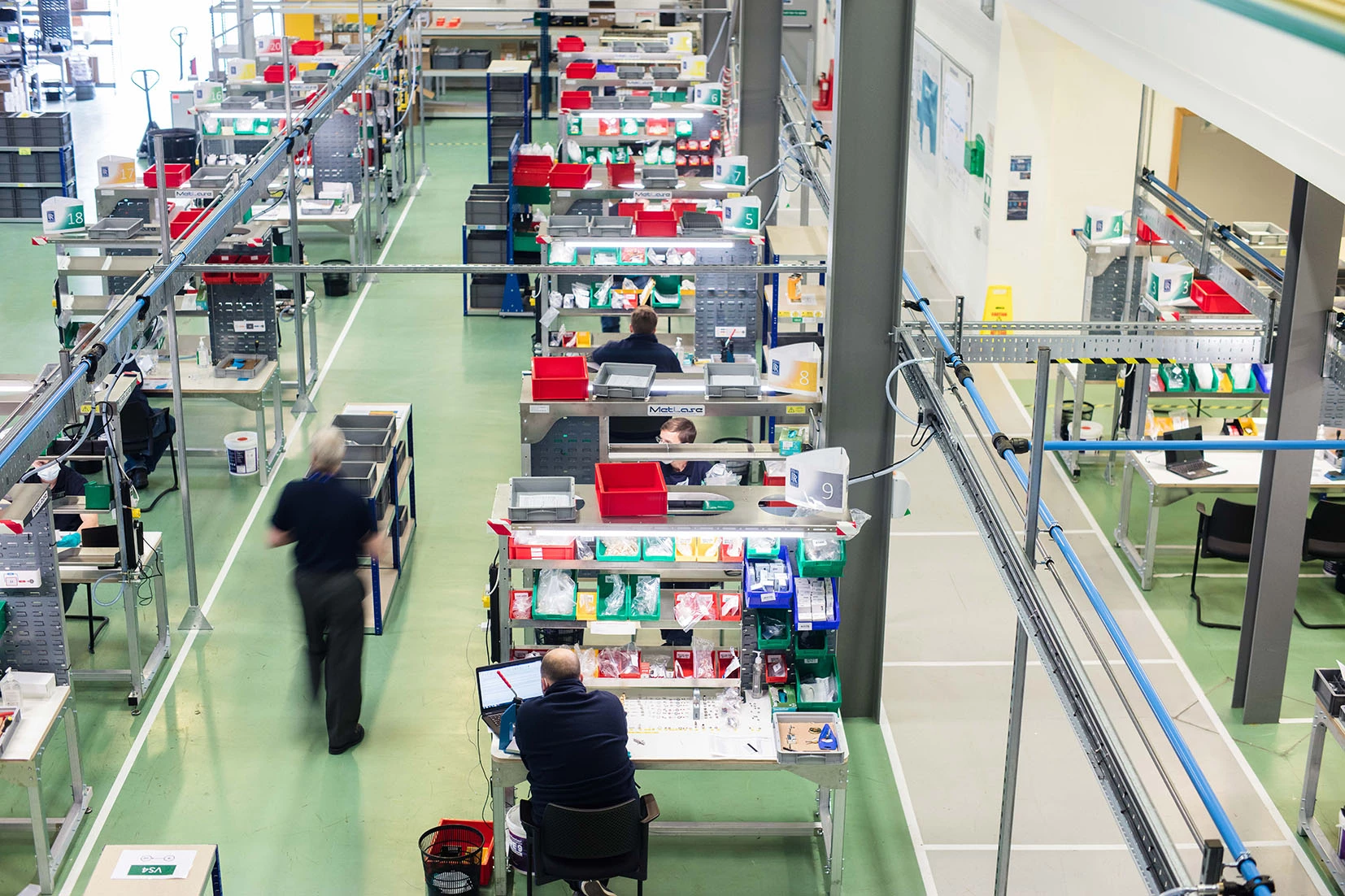
Member Article
MetLase chief urges industry to ‘flex’ its technologies to support Covid-19 recovery
Creating flexible manufacturing facilities will support industry’s recovery from Covid-19 according to the head of one of the UK’s leading engineering experts.
Steve Dunn, Managing Director of Rolls-Royce and Unipart joint venture business MetLase, believes the firm’s pioneering work in the VentilatorChallengeUK consortium highlights how technology proven in the aerospace sector has been used in other sectors to help build the country’s manufacturing resilience and support reshoring activities that are slowly picking up pace.
The experienced engineer says the rapid deployment of adaptive manufacturing processes enables companies to reconfigure their factories to keep their workforces safe, accelerate and standardise training and processes and support diversification into new sectors to mitigate unprecedented drops in volumes.
The rallying call comes after his firm played a pivotal role in the nationwide effort to produce more ventilators for the NHS, providing critical design and manufacturability support for consortium partners and production of 72 bespoke manufacturing workstations for Rolls-Royce’s Bristol facility.
These were produced in just ten days, which was significantly faster than it was going to take to purchase and install standard benches.
“Industry hasn’t really seen anything like the sudden changes the pandemic has thrust upon it and there is now a massive need for manufacturing to be more flexible and rapidly adapt to a changing economic picture,” explained Steve.
“Horizontal innovation, where we take core technology and processes developed in one sector and transfer them to deliver a solution in another, is very much in demand.”
He continued: “This is supported by an outstanding engineering team that we can mobilise quickly, with more than 500 years’ knowledge and experience between them - a very powerful source of competitive edge and one we are now putting to good use with exciting new projects in automotive and medical.”
MetLase, which is part of Unipart Group alongside Instrumentel and Park Signalling, specialises in the manufacture of world-class tooling, intelligent fixturing and components, bringing lead times of months down to hours or days.
The company currently employs 30 people at its facility on the AMP Technology Centre in Sheffield and works across automotive, aerospace and, increasingly, in scientific equipment and pharmaceuticals, with over £1m of new contracts secured in the UK, Australia, the EU and the US.
It is also seeing significant growth in the need for tailored digital solutions and in-fixture automation, giving manufacturers essential data at all stages of the process, enabling continuous improvement, machine learning and artificial intelligence.
“Faster, more intelligent manufacturing that delivers data is what industry is demanding and we are at the forefront of how we can turn a traditional fixture or tool into an intelligent component,” added Steve.
MetLase is hosting a special webinar to support manufacturers to increase their resilience and ability to adapt to the current situation so they can recover from Covid-19. This will be held live on 30th July at 3pm (GMT) and you can register to attend at https://bit.ly/flexiblemanufacturing
For further information, please visit www.metlase.com or follow @metlase on twitter
This was posted in Bdaily's Members' News section by Russ Cockburn .
Enjoy the read? Get Bdaily delivered.
Sign up to receive our popular Yorkshire & The Humber morning email for free.