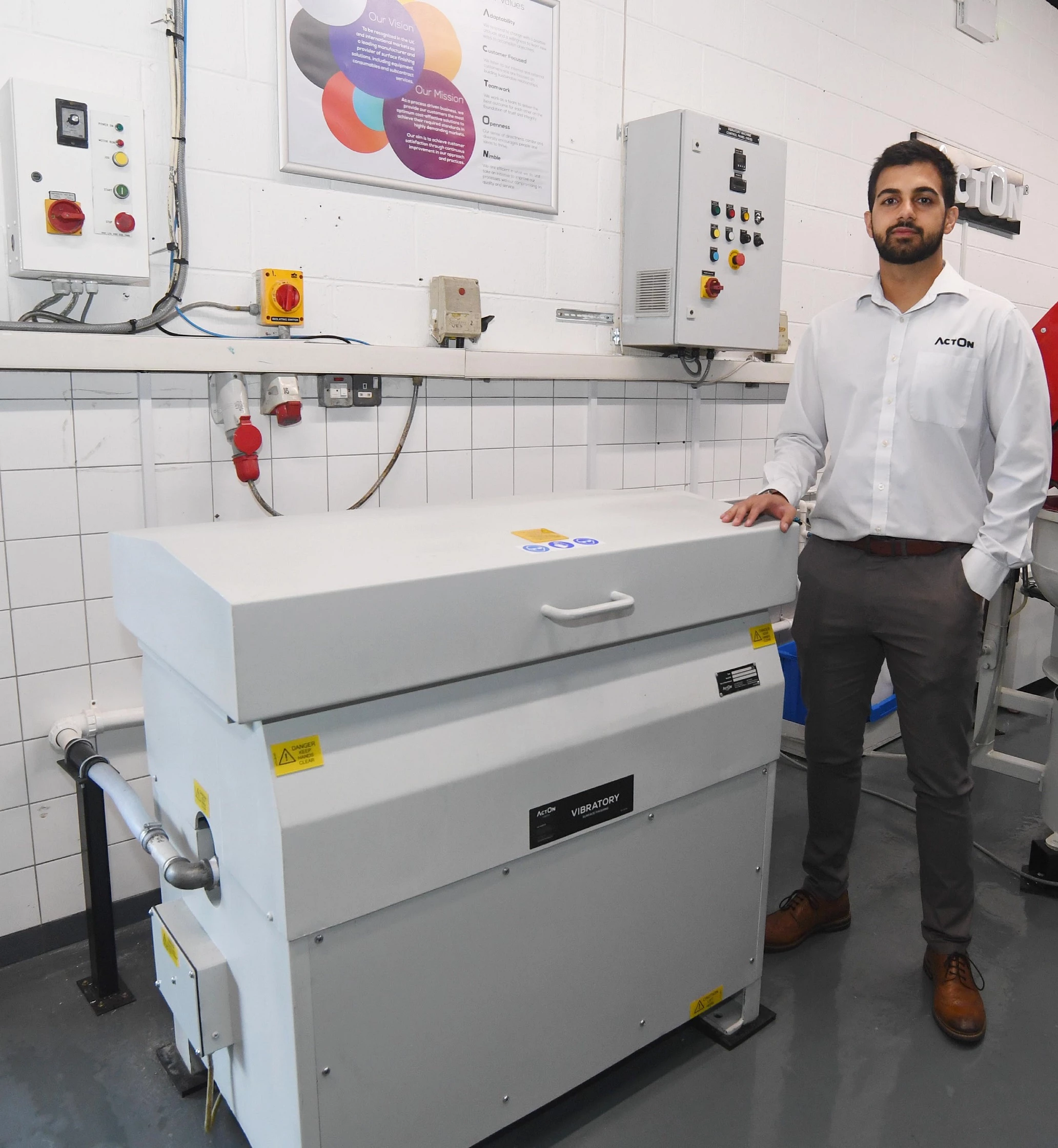
Partner Article
Coventry engineering firm helps aerospace giant clean up with cutting-edge technology
A leading engineering firm headquartered in Coventry has helped aerospace giant Rolls Royce clean up thanks to some cutting edge technology.
ActOn Finishing, based in Torrington Avenue, has installed a vibratory finishing system at Rolls Royce Bristol to improve its cleaning process and increase productivity – enabling the engine manufacturer to process three times more volume in a shorter time frame. The engineering firm was contacted by the manufacturer to look at improving cleaning during its shelling process, which leaves a build-up of ceramic slurry on the equipment used.
ActOn carried out live trials at its facility and found that the vibratory finishing machine was the right solution to clean parts quickly and consistently. The machine, designed and manufactured by ActOn Finishing, has now been installed at Rolls Royce Bristol, reducing the process time from 60 to 10 minutes and enabling the firm to clean three times more equipment at once.
The finishing machine has also reduced the firm’s water consumption while still achieving a cleaner finish. Sid Gulati, operations director at ActOn Finishing, said: “We have a long-standing relationship with Rolls Royce having done subcontract polishing for the company for a number of years.
“They contacted us about a problem that they were having with their cleaning processes, and although this kind of application was new to us, we were able to conduct trials and find a solution for the client. “We found that the vibratory finishing machine produced excellent results which Rolls Royce was very happy with.
“We installed the machine and provided training to members of staff and have already received some excellent feedback. “We’re very pleased that we have been able to achieve such a positive result for Rolls Royce Bristol, streamlining their processes and increasing their productivity.” Henry Illsley, shell process engineer at Rolls Royce Bristol, said: “ActOn were quick to develop a solution for the shell cleaning system.
“The machine has improved our throughput significantly and we are pleased with the quality of machine that they have manufactured and installed. We look forward to working with ActOn on future collaborative projects.”
This was posted in Bdaily's Members' News section by Matt Joyce .