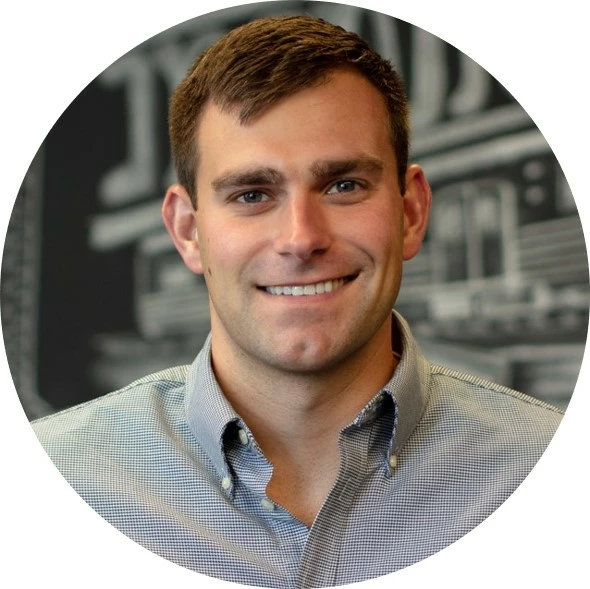
Member Article
How to Start a Continuous Improvement Programme: 6 Simple Steps for Your Supply Chain
By Ben Steffes, Director of Strategy Services at Coyote Logistics
Implementing a continuous improvement programme in any business seem like a daunting project, but the benefits far outweigh the effort. Small, incremental changes can produce dramatic results.
Despite the COVID-19 pandemic, organisations must look to continuously improve. A commitment to a consistent, structured approach can help supply chain operations become more efficient.
What is continuous improvement?
Continuous improvement is a proactive approach to superior customer service which prioritises the elimination of waste and relies on active employee involvement to develop solutions to challenges, as they arise. Continuous improvement involves six distinct phases that seek small improvements in processes and products, with the objective of increasing quality and reducing waste. These 6 phases of continuous improvement are:
- Assess the current situation – Acknowledging the current state of your operation will make it easier to distinguish the pain points and then implement improvement strategies.
- Identify the main problem – The problem should address the discrepancy between where you are and where you want to be.
- Establish a target goal – Before mapping out a solid improvement strategy, it is important to establish your target goal(s), so you know what to work towards and how to measure progress.
- Map out a strategy - Including team members in the strategy mapping process is incredibly important, as it increases buy-in and boosts morale.
- Measure effectiveness – In order to gauge the effectiveness of your improvements, it’s important to analyse the effectiveness of your actions in relation to your target goals. You should track projects and measure improvements on a monthly, quarterly, and annual basis to maximise the impact of the continuous improvement process.
- Celebrate success – Celebrating the success of your new procedures and strategies is a significant phase of the continuous improvement process. This is also an opportunity for strengthening your organisation while fostering a team-oriented culture comprised of individuals committed to ongoing improvement.
Small Changes, Big Results
Some continuous improvement projects are large-scale operational overhauls, but a vast majority are small, incremental tweaks implemented by core team members within each department, rather than throughout the entire organisation. A successful continuous improvement programme doesn’t rely on leadership making big strategic decisions, but instead enlists front-line employees and managers to implement small improvements that snowball into measurable results. Small tweaks driven by front-line employees are the basis of a successful continuous improvement programme.
Commitment is the Key to Success
It is important to remember that the continuous improvement process depends on just that: improvement that is continuous in nature. An explosion of quick wins, while exciting, is not a compelling reason to abandon the structure. The programme’s structure is a key driver to its success in the long term. You can experience the same dynamic results, with minimal to no additional programmes, services, or employee headcount. Creating a culture of continuous improvement within your organisation takes commitment, but it is possible, and the results are likely worth it.
This was posted in Bdaily's Members' News section by Coyote .