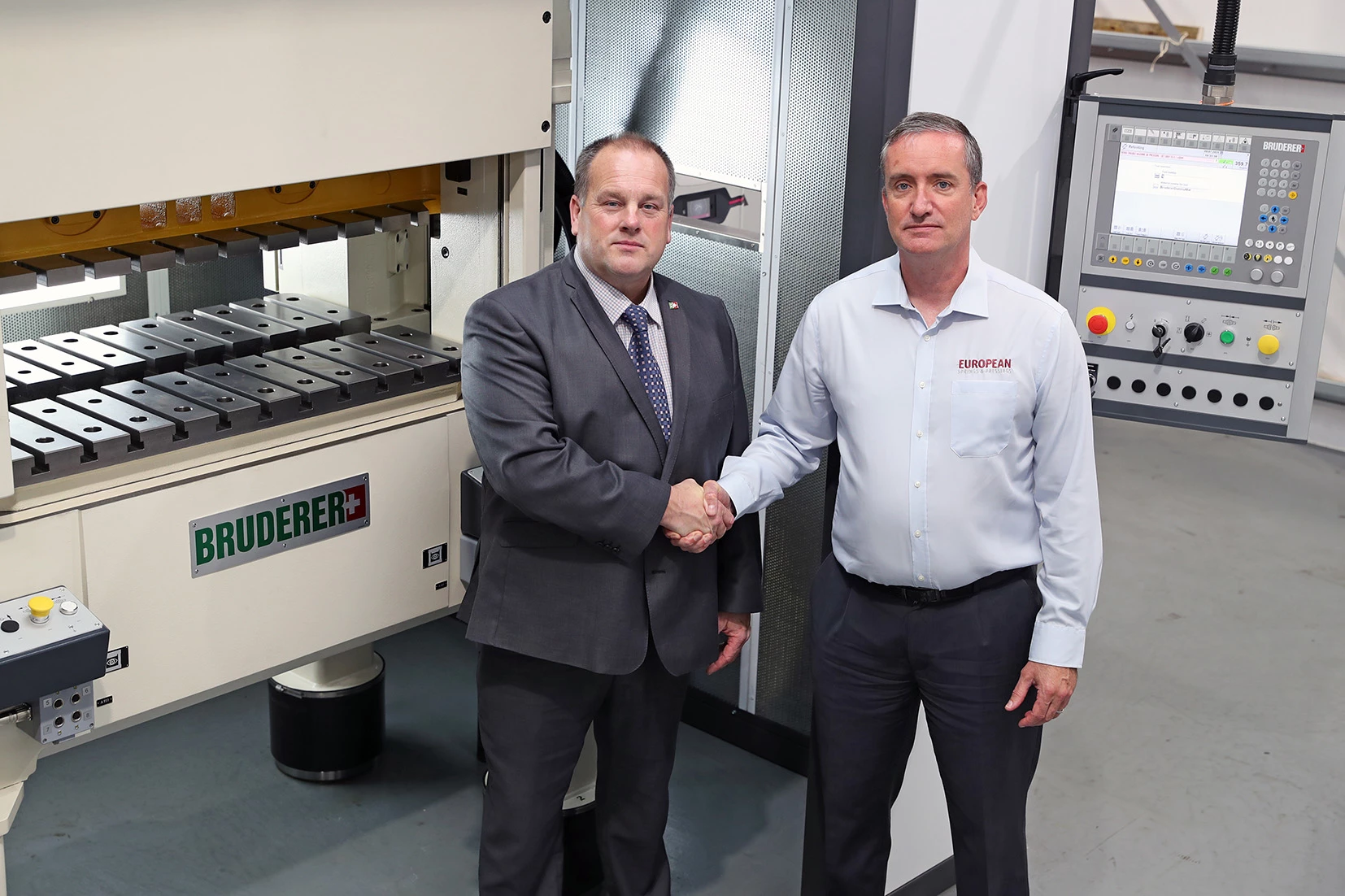
Member Article
New Bruderer press is jewel in the crown of European Springs & Pressings’ £700,000 press shop redevelopment
One of the UK’s leading manufacturers of precision springs, wire forms, pressings and assemblies has completed the relocation of its new press shop with the addition of a new, high-speed precision Bruderer press.
European Springs & Pressings Ltd, which supplies customers in the automotive, aerospace, building products, medical and nuclear sectors, has installed a BSTA 410-110B2 and high precision servo feeder to help it increase capacity and target more than £1m of new opportunities.
Fitted with the latest press and tool monitoring technology, the machine’s expansive 1100 mm bed, production speeds of up to 1600 strokes per minute and fully adjustable stroke between 16 and 47mm, makes it an ideal addition for the Beckenham-based firm and means it can be used for pretty much every product it makes.
Continuing its policy of long-term investment in cutting-edge, innovative technologies, the acquisition is the final stage of a dynamic £700,000 project that has involved the construction of a dedicated 6000 sq ft press shop, which is set to deliver 20% efficiency gains and more streamlined production cells.
Stuart McSheehy, Managing Director of European Springs & Pressings, commented: “Our relationship with Bruderer UK goes back more than 15 years and this will be our third new machine we’ve taken from Adrian Haller and his team.
“The Swiss stamping technology is the best in the world when it comes to precision, achieving tolerances and delivering flexibility, and this new BSTA 410-110B2 will be the real jewel in the crown of our new press shop.”
He continued: “A long press bed is ideal for satisfying the increasing demand from customers for longer press tools that accommodate more progressions and more complex shapes. We also required a machine capable of giving us versatility when it comes to strip width and material thickness.
“Working with the Bruderer team, we made the decision to spec the machine up with a state-of-the-art servo feeder to help us automate some of the jobs and a high-end multi-head MicroCoat lubrication system for greater performance, whilst tool protection technology, press force monitoring and acoustic booths were also added.”
European Springs & Pressings remained operational throughout Covid-19, diversifying its product range to produce components that went into surgical masks, other medical devices and the power generation supply chain.
Due to the diverse nature of its markets, the company has enjoyed rapid growth since the easing of lockdown and is on course for a record £11m sales in 2021, which should create more than ten jobs.
The new press shop was critical to this expansion and the business was again assisted by Bruderer’s centre of engineering excellence in the UK in the relocation of presses, ensuring that production was still able to meet day-to-day targets.
Stuart went on to add: “This project was two years in the making and highlights the strong partnerships we have with our suppliers, especially Bruderer UK, who we asked to provide engineering services for the decommissioning, relocation and recommissioning of two of its high-speed presses and one, 160-tonne Zani machine.
“The latter was an especially complex move and had to be taken from its existing position on its side and then erected into its new location in the machine shop. Having a company with such a strong product knowledge meant we were confident that this process would not affect the press in the long-term and the relocation was completed with only one machine ever out of action at any time.”
Adrian Haller, Managing Director at Bruderer UK, concluded: “We have built a strategic relationship with European Springs & Pressings, and this is reflected in the trust it placed in us to support its press shop relocation.
“The installation of the BSTA 410-110B2 is a clear indication of the precision markets the company is going after. In particular, the control technology added to the press provides automatic ram shut height adjustment while the machine is under acceleration and deceleration loads, giving it guaranteed process stability and pinpoint repeatability.
“What is a really pleasing element of this partnership is how apprentices are being trained on the latest high-speed presses, futureproofing their careers for years to come.”
For further information, please visit www.europeansprings.com or www.bruderer.co.uk. You can also find out more on high-speed presses by following @brudereruk on twitter.
This was posted in Bdaily's Members' News section by Russ Cockburn .
Enjoy the read? Get Bdaily delivered.
Sign up to receive our popular morning London email for free.