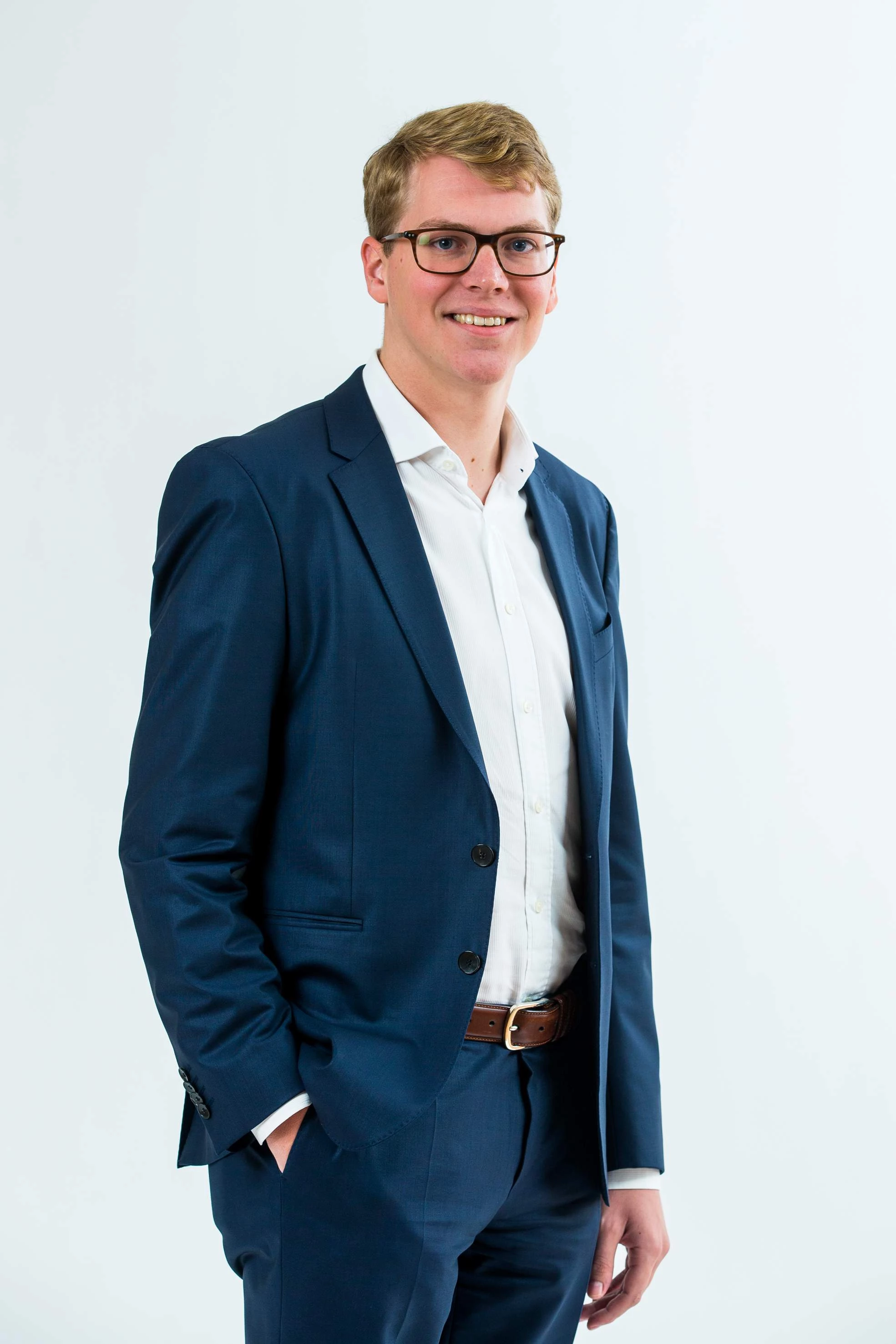
Member Article
Visual display installation and maintenance – breaking down the complexities
One of the most exciting things that we’re seeing around video walls is peoples’ changing perceptions towards them. Video walls are no longer simple signage, they’ve come to be thought of as having a critical impact on a business’ functionality. As their use continues to rise in popularity, it is important businesses understand both the technology’s potential, but also the maintenance that goes on behind the scenes.
Effective mounting and installation
Mounting and installation can be a major task, especially for large sizes, unusual shapes, or awkward locations. The ecosystem that comes with mounting is key, because ultimately businesses buy an experience, not just a technology, and when you buy a video wall you want assurance that your vision is going to come to life.
Installation conditions will never be perfect. So, when discussing effective installation, what we are really talking about is the customer need for predictable outcomes. The way to provide these outcomes is through product design and partnerships with trusted and pre-validated third-party installers, mount providers, and system integrators, as skilled labour is a big part in minimising risk.
Mechanically and optically, it is possible – and desirable – to build in systems which can fine-tune the installation process. With our LED video walls for example, you have optical seam compensation, whereby you take a picture with a camera within the video wall and an algorithm can calibrate and steer the LEDs at the edge of the wall to get a perfect picture. On a mechanical level, you can build in physical adjustment points so you can give the installer the freedom to cue XYZ in the way that they see as perfection.
Maintenance and repairs don’t need to be excruciating
Post-installation maintenance and support can pose challenges, especially in the case of displays that operate 24/7. Ensuring the video wall looks at its best over years without deterioration requires adequate planning and design.
Quality deterioration is not simply a post-care issue. Deterioration has a lot to do with the product design process, and it’s something that begins with the quality of the materials you choose. Deterioration is particularly important in mission critical 24/7 applications. If you have any deterioration in the video wall of a power company monitoring the grid, you might not know when a neighbourhood loses power. That’s why component selection, strict quality processes and embedded redundancy are key in designing and bringing products to market.
When service interventions do need to be made, you want to make them as safe and quick as possible. Service diagnostics can now be run from the cloud for an entire fleet of video walls, so by the time a maintenance expert needs to go on-site, the issue has already been diagnosed.
In terms of physical servicing, you want to minimise the potential disruption to any operation. Being able to access the inside of an LED video wall from the front and back, as well as motorised extraction for the quick and safe removal of parts is one way this is already being done. In less than a minute an engineer can safely swap an LED module out in a way that is as unintrusive as possible.
Key takeaways
The technology today is advanced enough to ensure visual display installation and maintenance isn’t an obstacle for any business wishing to benefit from the technology. With adequate planning and support, a video wall display can be mounted and serviced over years with minimal disruption to the day-to-day, making the technology more readily available and accessible than ever before.
This was posted in Bdaily's Members' News section by Barco .
Enjoy the read? Get Bdaily delivered.
Sign up to receive our popular morning London email for free.