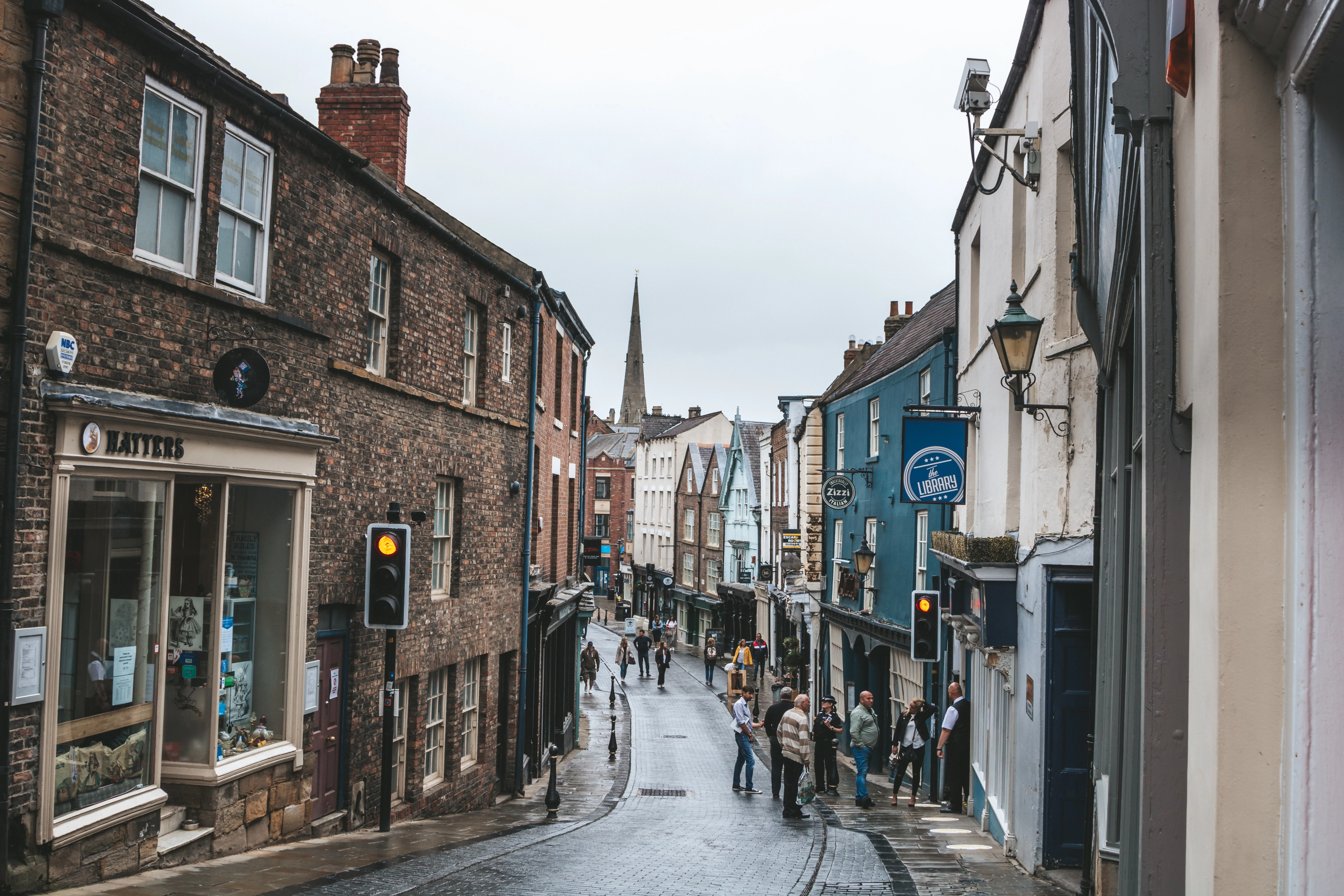
Durham's Apex Core celebrate success in Canary Wharf
A speculative investment that has rapidly become an industry game-changer is celebrating another huge contract success. Apex Core is manufacturing 450 prefabricated utility cupboards (PUCs) for a luxury apartment development, which will be one of the highest buildings in London’s financial district.
The units, all manufactured in Durham City, are for the “Aspen” scheme in Consort Place, Canary Wharf. The contract was awarded to Apex Core by ARK, part of JRL Group, which is overseeing the high-quality mixed-use project.
Apex Core sales director, Paul Hopps, said: “Apex Core units are perfect for apartment builds and urban development, particularly in the cramped confines of most London sites, arriving assembled and ready to “plug in”.
“When we invested £500,000 in creating the largest specialist PUC manufacturing facility in the UK three years ago, it was barely even a fledgling industry, but with developers recognising the huge time saving benefits they offer, they’re revolutionising the industry.
“We are delivering Core units to enormous developments all over the capital, which is really embracing the concept, but the rest of the UK is coming around to them too, so we expect we’ll need to expand operations in 2023.”
Apex Core designs, develops and manufactures prefabricated utility cupboards – a central hub for a home’s heating, ventilation, electrical, communication and metering services.
The Aspen is a £450m 900,000 sq m development including two residential towers of 65 and 35 storeys, together with a 4-star, 21-storey hotel, all linked by a central public square at ground floor. At 217 metres, The Aspen will be one of Canary Wharf’s tallest residential towers. The development has 450-apartments, a spa and a spectacular sky bar on the 63rd floor.
It is a major win for the firm, which was launched three years ago, with Apex Wiring Solutions owners, Dave and Mike Lewis, investing over £500,000 in the facility at the firm’s HQ in Durham City.
Apex Group MD, Dave Lewis, said: “When we invested in modular wiring manufacturing, that was in its infancy, but it very quickly became the norm as developers realised the many time and cost saving benefits it offered. PUCs are the same they are a faster, safer and more sustainable solution than traditional utility installation methods.
“London has embraced the technology, with PUCs increasingly becoming the norm, but with the rest of the UK waking up to their potential, I can only see us growing further in the short to medium term.”
To date, the firm has delivered over 6,400 units to sites, as the construction sector embraces the benefits that modular units, constructed off-site and delivered ready to install, offer.
By Mark Adair – Correspondent, Bdaily
- Add me on LinkedIn and Twitter to keep up to date
- And follow Bdaily on Facebook, Twitter and LinkedIn
- Submit press releases to editor@bdaily.co.uk for consideration.
Looking to promote your product/service to SME businesses in your region? Find out how Bdaily can help →
Enjoy the read? Get Bdaily delivered.
Sign up to receive our daily bulletin, sent to your inbox, for free.