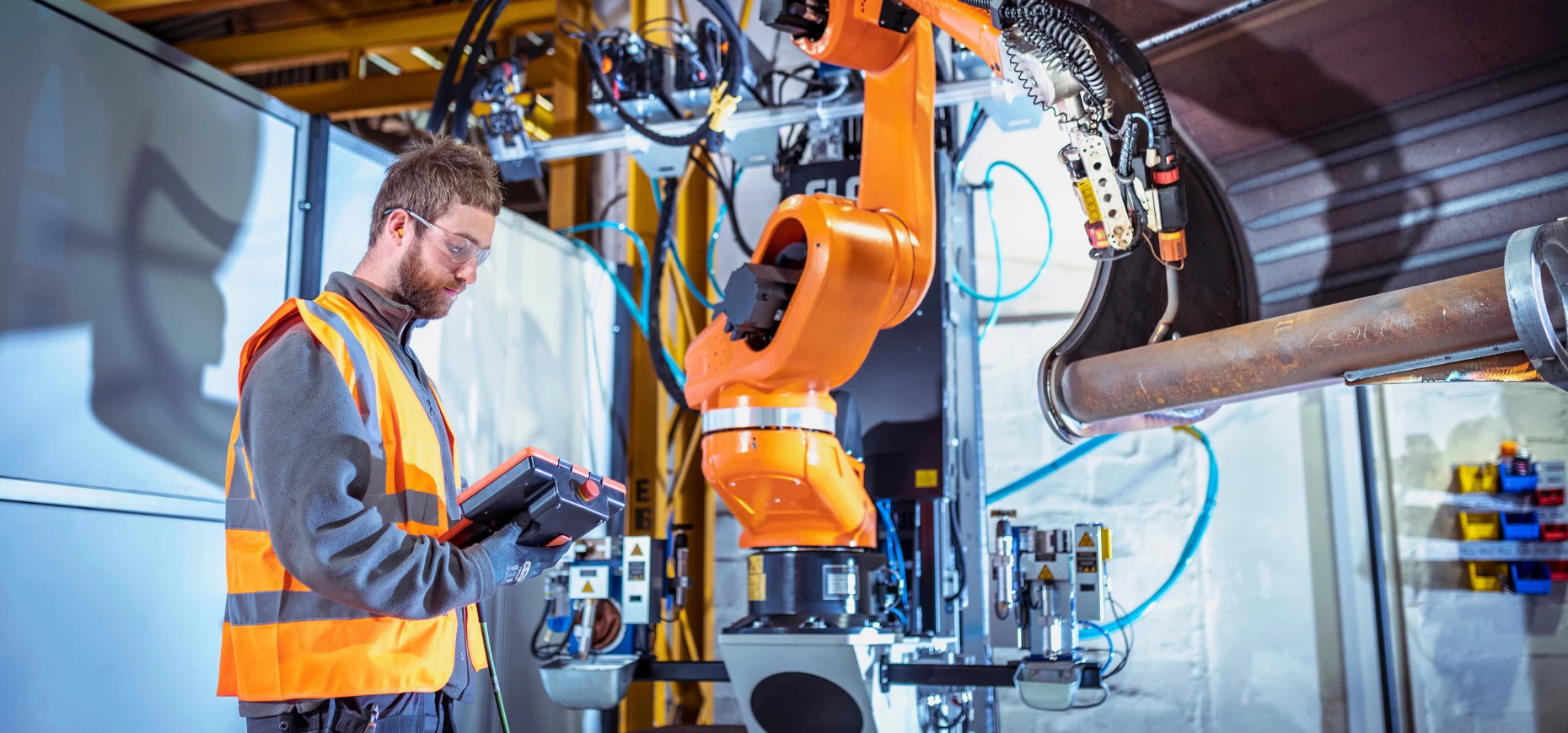
Northumberland manufacturer invests in ‘next generation’ of robotic automation
A major North East based bucket and coupler manufacturer, Miller UK, has significantly bolstered its manufacturing capabilities through upgrading its suite of ‘state-of-the-art’ welding robots significantly increasing production and the safety of its workforce.
With headquarters in the Cramlington, and operations across the globe, Miller has invested in five new robots commissioned and already in full operation, allowing the firm to significantly improve its welding speed and deliver 100 per cent weld consistencies on its product range.
The new robots are developed by ‘industry leaders’ in welding and automation, CLOOS and include two different model ranges, QRC 410-2.0, ideal for welding attachments for machines up to 45 tonne and two QRC 350-E models, capable of handling attachments for machines up to 100T.
The company first invested in its welding robot range in 2018, with the first installation of the smaller robots. Recognising the value of these machines, Miller has now installed the latest range of these models with the introduction of two of the larger sized machines which doubles the company’s production capabilities.
And the business believes that it is the very first of its type across the globe to have such advanced robotic welding machinery capable of producing buckets with a width of up to 3.2m with the ability to hold up to 4.5T of material which the larger robots offer.
James Ross, Commercial Director at Miller, commented: “Manufacturing technology has always been a priority and it is very important that Miller continues to invest in the next generation of welding equipment and robotic automation which can transform the quality to consistent market leading levels.
“This will be recognised by our customers in terms of product durability and performance in the field.
“With minimal production downtime required, and the ability to operate for extended periods of time, this has significantly increased our manufacturing capabilities, particularly to produce much larger buckets for extreme applications, to meet our demand and significantly reduce our lead times for customers.”
Gregg Hudson, Global Manufacturing Leader, added: “The new robot really does step our production capabilities up to the next level. The weld finish achieved from this machine is exceptional – and like nothing else you will see on the market – as we continue to drive our quality standards, which is what we are known for.
“It is an exciting time at Miller for our staff on the shopfloor to work with the new machinery and learn the next generation of pre-programming welding automation techniques to operate the equipment, whilst continually developing their manual skills.”
By Matthew Neville – Senior Correspondent, Bdaily
- Add me on LinkedIn and Twitter to keep up to date
- And follow Bdaily on Facebook, Twitter and LinkedIn
- Submit press releases to editor@bdaily.co.uk for consideration.
Looking to promote your product/service to SME businesses in your region? Find out how Bdaily can help →
Enjoy the read? Get Bdaily delivered.
Sign up to receive our daily bulletin, sent to your inbox, for free.