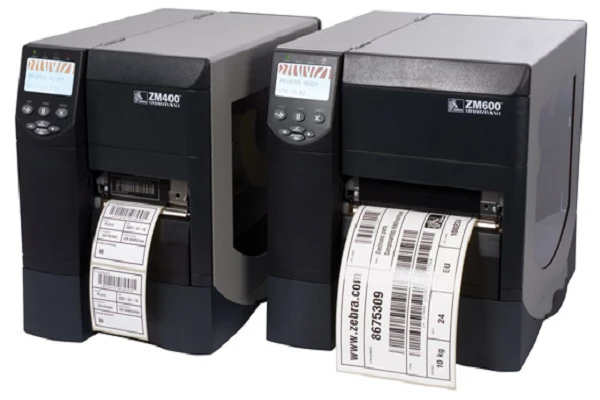
Partner Article
Direct Thermal vs. Thermal Transfer Printing: What’s the Difference?
Both direct thermal labels and thermal transfer labels have their own equally long lists of benefits and practical applications. Depending on your requirements, one (or both) could be ideally suited to the job, and prove a highly cost-effective investment.
But what are the main differences between these two types of labels, and what primary purposes are they designed for? Are direct thermal labels and thermal transfer labels interchangeable, or are they designed with different applications in mind?
Direct Thermal Printing
Direct thermal printing is a type of printing that involves the use of a special type of medium, as opposed to conventional labels or paper. Direct thermal printers simply apply heat to the material, which is coated in leuco dye. Completely invisible prior to being heated, leuco dye is converted to a different chemical form when heat is applied and creates the required effect on the surface of the material.
What this means is that the printer itself does not contain or use any ink whatsoever, as the ‘ink’ is already on the label itself in an invisible form.
The Benefits of Direct Thermal Printing
One of the biggest benefits of direct thermal printing is its cost-effectiveness. As the printers themselves do not need to house any ink or dye, they can be made extremely compact and portable in nature. No consumables are needed (other than the labels themselves), which can make direct thermal printing much cheaper than many comparable alternatives.
In addition, it is also an extremely fast and convenient approach to printing. Direct thermal printers are the tools of choice for printing shipping labels, issuing parking tickets, printing tickets on trains and so on. Where on-the-spot printing is needed as quickly, efficiently and reliably as possible, direct thermal printing is the preferred option for many.
The only downside to thermal transfer printing is how the material that contains the leuco dye can be damaged, if exposed to high temperatures or abrasions. In addition, a label printed using the direct thermal method may not have the same extensive lifespan as a more conventionally printed label.
Thermal Transfer Printing
Meanwhile, thermal transfer printing adopts a more conventional approach to the printing process. Rather than utilising materials treated with leuco dye, thermal transfer printers are compatible with a broad range of standard materials.
This is because the printer itself houses the ink/dye used to create the required effect on the printed medium. Heat is applied to a special printing ribbon housed within the device, which can be purchased in a wide variety of different colours.
The Benefits of Thermal Transfer Printing
Thermal transfer printing is often the preferred option where the lifespan of the result is more of a priority. The results of thermal transfer printing are extremely precise and robust in nature, with a longer lifespan than direct thermal labels.
This makes thermal transfer printing ideal for things like barcodes, safety labels and certification labels – anything that needs to display information clearly and concisely for a long time. The printed labels are comparatively resistant to abrasion and exposure to heat, making them useful for most environments. In addition, thermal transfer printing can be more cost-effective than some conventional approaches to printing (such as laser printing, dot matrix printing, etc.) The only downside (in comparison to direct thermal printing) is the requirement for additional consumables for the printer to work.
Some types of thermal transfer printers are also not as compact or portable as direct thermal printers, as they need to house a special printing ribbon to work.
This was posted in Bdaily's Members' News section by iCONQUER Ltd .