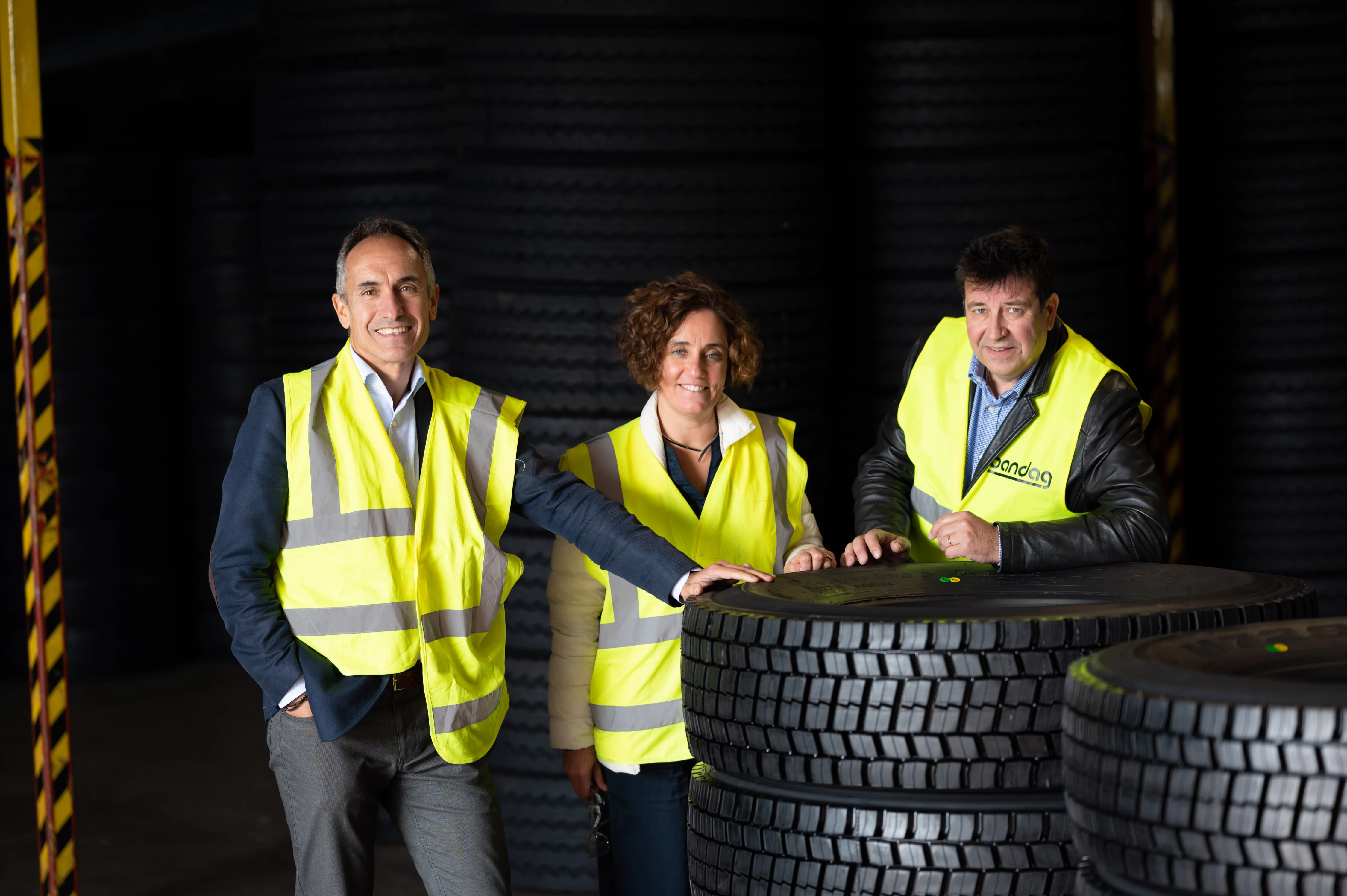
Partner Article
Bridgestone’s multi-million-pound investment makes retread range hot property
Bridgestone’s commitment to its retread tyre offering has been emphatically underlined with a multi-million-pound upgrade of its range, which will further expand its manufacturing processes and lead to more ‘hot’ products being produced than ever before from its Lincolnshire factory.
Under the new ‘Bandag Hotread’ name, Bridgestone’s retread solutions will become some of the most advanced in the UK, featuring 17 new products being manufactured from its Bourne-based Bulldog plant.
In a boost to the UK Manufacturing sector and a triumph for the commercial transport industry, Bandag Hotread will cover the HGV (Heavy Good Vehicle), bus and coach markets. It will see a greater shift in emphasis from cold to hot-cure products, in response to demand from commercial customers.
The significant investment will see new state-of-the-art machinery brought into Bridgestone’s Bulldog Factory in Bourne, Lincolnshire and will transform Bridgestone’s retread offering, which is a sector that currently accounts for around 24% of commercial tyres sold in the UK per year.[1]
In 2022 alone, Bridgestone’s Bulldog Factory recycled 520 tonnes rubber dust and 4,400 tonnes’ worth of scrap tyres. This equated to savings of 4 million litres of oil, 2,000 tonnes rubber and 900 tonnes of steel and close to 4000 tonnes of saved CO2 emissions versus equivalent production of new tyres.[2]
Retread tyres use less than one-third the amount of raw materials used in new tires and enable the reuse of other tyre components, such as the casing. The retreading solution significantly contributes to the reduction of discarded tyres as well as the reduction of waste in communities.[3]
David Almazán, Bridgestone’s Commercial Business Unit Director, Bridgestone North Region, said: “There is a move towards the lowest total cost of ownership of product, combined with increasing awareness of the need for a more sustainable and circular economy where recycling is standard.
“Bridgestone is fully committed in this regard, which is why we have made such a significant expansion of our retread range. A sustainable future fits with our company ethos, and retread is economically good for the customer and takes a central role in our commitment to develop sustainable tyre technologies and solutions that preserve the environment for future generations.”
Bridgestone also operates a fast, efficient, nationwide casing collection service that ensures casings are swiftly collected from customer locations in a safe and compliant fashion with full traceability, and ensures maximum value is extracted from this key asset.
All retreaded tyres from Bridgestone’s Bulldog Factory and Bandag franchises are not only a safe and reliable alternative to a new set of tyres, but also a solution for reducing fleets’ tyre related costs per kilometre. This proposition applies also to retreads made from Bridgestone and Firestone tyre casings – for which the retreadability by Bandag is also 100% guaranteed.
Bridgestone’s retread investment represents a major part of its mission to continue to provide social and customer value as a sustainable solutions company toward 2050. Retread also embodies Bridgestone’s E8 Commitment – a set of eight areas (Energy, Ecology, Efficiency, Extension, Economy, Emotion, Ease, Empowerment) which provide a compass and guides Bridgestone to do business in a sustainable way. The commitment to retread aligns perfectly with the “Efficiency,” “Energy,” “Ecology” and “Economy” values in the E8 philosophy.
For more information about Bridgestone’s commercial tyre offering, visit http://www.bridgestone.co.uk/truck-and-bus/
This was posted in Bdaily's Members' News section by Russ Cockburn .